Assured Micro operate within a full quality management system which covers all areas of the business, from testing protocols, to goods received to CAPA and OOS investigations. The Quality System is defined and controlled by both the Quality Manual and the SOP system which governs everything from sampling technique to the training system. The Quality Manual is available for review upon request and sets out Assured Micro’s Quality Policies.
Each operator has an individual training record which contains a training plan and details all training performed. Training records are regularly reviewed to ensure compliance and refresher training in key areas such as GMP documentation is provided to all staff. Client specific training is also performed with all staff to ensure Operators are aware of all client specific requirements.
Goods received are managed by the Quality System with a detailed material control procedure which covers approved suppliers, material approval and re-testing of reagents. All materials ordered are managed using the Control of Materials SOP where all items are thoroughly checked to ensure suitability before use. Assured Micro also has a supplier certification programme and all critical suppliers are subject to Quality Approval.
The Quality department carry out regular compliance audits of various aspects of the quality system including logbook control and 6 monthly trending of non-conformances. An annual report is also produced which contains trending of all non-conformances, details of all quality improvements made that year and recommendations for improvements for the coming year.
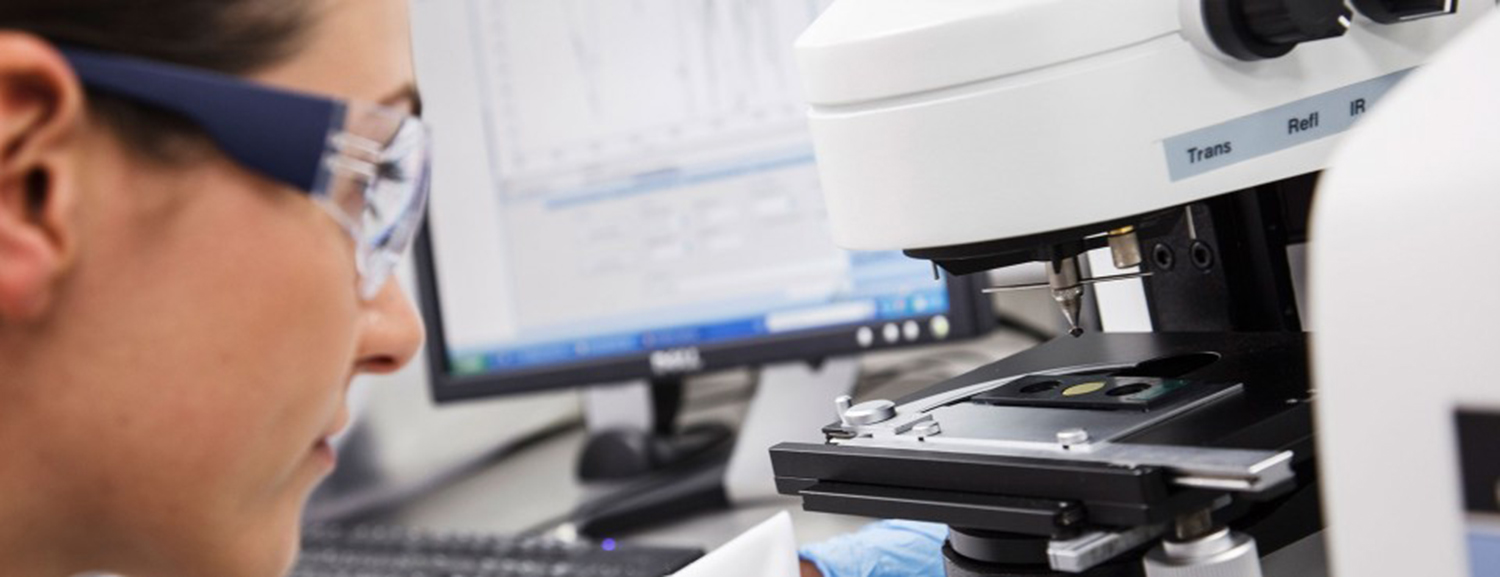